Hands On with the Twotrees TTC 450 CNC Router
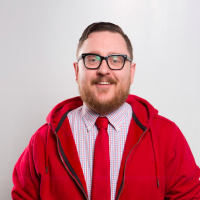
Written by Nick Biederman
We’ve taken a fairly in-depth look into the world of hobbyist laser cutters over the last year. Today we’ll be shifting gears and looking at a desktop-sized CNC router from Twotrees, the TTC 450. CNC routers are conceptually similar to laser cutters but with a major difference in how they cut. Some key differences include:
● Method of cutting: Laser cutters use powerful focused light while CNC routers use a spinning router bit.
● Work holding: Since a moving router bit is in contact with the material, CNC routers require more rigid work holding than laser cutters.
● Kerf thickness: The kerf - or cut thickness - on a laser cutter can generally be ignored, while CNC routers can have a large kerf. The kerf size of a CNC router is determined by bit selection.
● Materials: Some materials that are unsafe to process on a laser can be processed on a CNC router, and some materials that are easy to process on a laser can’t be processed on a CNC router
● 3D capability: CNC routers work great for 2.5 and 3D projects, while laser cutters are better suited for 2D projects.
● Software toolchain: CNC routers generally require a more complex CAM process than laser cutters.
Opening the TTC 450
The TTC 450 from Twotrees is a small, desktop CNC router
We’ll talk about many of these points in detail, but let’s start by taking a look at the router. It comes nicely packaged in layered foam, just like the Totem S. All the tools needed to assemble it are included, and the instructions are easy to follow. It took me about an hour to assemble.
All the parts come packaged in foam. 3 of the 4 layers can be seen here.
The machine surface is made from MDF (Medium-Density Fiberboard) with a grid of nuts to use for work holding. The MDF won’t damage router bits if you cut too deep, but I wouldn’t treat it as a sacrificial work surface.
The spindle is a simple 80-watt DC motor. This is a bit less powerful than some other hobbyist CNC spindles and routers but will work for light cuts in soft materials, making it a good choice for newer users.
The 80-watt spindle.
It comes with several cutting bits, including a 3mm up-cut end mill, a 90-degree V tool, and several 30-degree V tools. The 3mm end mill is useful for pockets and perimeter cuts. The 90-degree V tool can be used for lettering and other engraving. The 30-degree V tools are meant for fine engravings, such as small plaques or PCBs. Like a lot of the TTC 450, these are mostly useful for beginners. They’ll work well for figuring out the basics of the machine and you won’t be too upset when you break them, but once you’ve worked out the kinks I’d recommend buying carbide end mills. A 6mm collet is also included.
Several bits are included, ensuring you don’t need to buy anything else to make your first cuts.
The rigidity is adequate for the included spindle. It’s unlikely you’ll run into issues with rigidity before exceeding the capabilities of the spindle.
While a pair of safety glasses is included, I would highly recommend picking up a pair of quality safety glasses before using the machine.
Testing the TTC 450
With an 18” square working surface, the TTC 450 is best suited for small projects. There’s a small piece of plastic included, so we’ll start our tests with that.
As mentioned above, work holding is important when working with CNC routers. The TTC 450 comes with several toe clamps and bolts to hold them down. I used a hold-down on each corner and tightened the bolts with the included wrench. While the design of the hold-downs isn’t as secure as other work-holding options I have used, it'll work great for this machine. I think you’d stall the spindle before the hold-downs failed.
I used 4 of the 6 included hold-downs to mount the plastic.
I then installed the included 3mm end mill and used the included zero plate to zero the Z axis.
With the material in place, I switched over to my laptop to get my toolpaths ready. The digital side of the CNC workflow can be divided into 2 parts: Computer-assisted design (CAD) and computer-assisted manufacturing (CAM). CAD is the process of designing the shapes that will be cut. CAM is the process of generating toolpaths and G Code from a digital design. Twotrees recommends Easel, which has both CAD and CAM functionality. There are a number of other tools available for both CAD and CAM, but we’ll take Twotree’s recommendation and use Easel.
Easel’s web based interface is simple and intuitive to use.
Easel is a web-based software package with free and paid tiers. A 30-day trial of the paid tier is available. The paid tier has some very useful features, like V Carve capability, but the free version works for the test we’ll be doing today. We’ll look at the details of Easel in a future article. For now, I used the CAD functionality to draw an oval with the text “TT450” in it and used the CAM functionality to generate tool paths and G Code. It wasn’t until I finished cutting the piece that I realized I left out the “C” in TTC 450. After using the simulation tool to ensure my toolpaths look good, I saved the G Code to a microSD card and installed it in the TTC 450. You can also stream G Code from a computer to the TT450 using Candle or Universal G Code Sender.
This was my first time using Easel, though I have used several other CAD and CAM tools in the past. The interface was fairly simple and intuitive. It didn’t take me long to figure out the basics I needed for this test cut. Finding the proper settings for the TTC 450 took some trial and error, but once I figured that out it was smooth sailing.
The TTC 450 in action
It took about 10 minutes to complete the cut. The results aren’t perfect, but solid for an entry-level cutter. While there are some chips hanging on to the finished piece - even after blowing it off with compressed air - the edges are sharp and clean. Different end mills would make a big difference in the end result, but the included one is a solid first-timer. Said included end mill is an up-cut end mill. Up-cut end mills work well for many materials, but a sharp O flute bit tends to give better results in plastics, like the one I used for my demo. We’ll explore end mill selection in a future article as well. You’ll notice some uncut tabs holding the finished piece into the plastic stock. This is necessary when using a CNC router to ensure the piece remains fixed to the bed after the perimeter is cut.
The results of my first test cut. The edges are sharp and clean, but there’s chips hanging onto the finished part.
My only real complaint is the lack of dust collection. Most CNC routers have a dust collection shoe that can be connected to a vacuum system. Out of the box the TTC 450 does not come with any dust collection. I’ll be exploring options to add dust collection in the future.
Without dust collection, the TTC 450 makes a bit of a mess.
The TTC 450 is a well made machine that’s great for hobbyists. Its low power spindle necessitates light cuts, but otherwise it’s a capable machine. I like that it includes everything you need for your first cuts, though some parts will be upgraded quicker than others as you get more comfortable with CNC routers. If you’re looking to dip your toes into the world of CNC routers, the TTC 450 is a great place to start.
Comments
-
Great info! Very interesting to get some insight on a product I'm not really familiar with at all personally.
-
Pumped for affordable cncs!!
-
Ohhhh! This is really cool! Great information to learn about the product.
-
thank you for the hands-on review with this cnc router! I was always wondering what it would look like to actually use one of these. back when i worked on stage sets and stuff in high school, something like this would be really cool to have for making props and whatnot.
-
I had been wondering about how well these work, thanks!
-
Nice article love learning
Categories
- All Categories
- 1 The Blog
- 1 What's Trending
- 7.7K The Community
- 3.1K General Discussion
- 130 New Members
- 832 Consumer Tech
- 215 Prebuilt PCs and Laptops
- 163 Software
- 31 Audio/Visual
- 51 Networking & Security
- 4 Home Automation
- 5 Digital Photography
- 13 Content Creators
- 29 Hobby Boards & Projects
- 80 3D Printing
- 83 Retro Arcade/Gaming
- 60 All Other Tech
- 353 PowerSpec
- 2.6K Store Information and Policy
- 148 Off Topic
- 52 Community Ideas & Feedback
- 612 Your Completed Builds
- 3.9K Build-Your-Own PC
- 2.8K Help Choosing Parts
- 326 Graphics Cards
- 334 CPUs, Memory, and Motherboards
- 141 Cases and Power Supplies
- 54 Air and Liquid Cooling
- 47 Monitors and Displays
- 90 Peripherals
- 64 All Other Parts
- 64 Featured Categories
We love seeing what our customers build
Submit photos and a description of your PC to our build showcase
Submit NowLooking for a little inspiration?
See other custom PC builds and get some ideas for what can be done
View Build ShowcaseSAME DAY CUSTOM BUILD SERVICE
If You Can Dream it, We Can Build it.
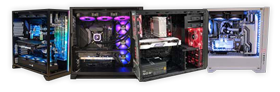
Services starting at $149.99