Solving Nozzle Clogs on Bowden Tube Style 3D Printers: A Comprehensive Guide
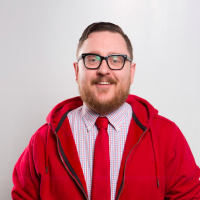
Written by Kyle Wall
Nozzle clogs are a common issue faced by 3D printing enthusiasts, particularly on Bowden Tube-style 3D printers. These clogs can hinder the printing process and result in subpar print quality. This comprehensive guide will delve into the causes of nozzle clogs and provide preventive measures to help you overcome this challenge and achieve optimal 3D printing results.
Nozzle clogs in 3D printers can stem from two primary sources: issues related to the filament and faults within the filament feeding and melting mechanism of the printer. Firstly, the filament itself may contribute to clogs if it contains impurities, such as dust, debris, or moisture, which can obstruct the smooth flow of filament through the nozzle. Additionally, filament consistency, such as variations in diameter or poor-quality filament, can lead to clogs. On the other hand, faults within the filament feeding and melting mechanism, including problems with the extruder, hot end, or Bowden tube, can disrupt the filament's journey from the spool to the nozzle, causing irregular extrusion and potential clogs. It is crucial to address filament-related issues and mechanical faults to minimize the occurrence of nozzle clogs and ensure optimal 3D printing performance.
To understand nozzle clogs, it is important to grasp the basic operation of Bowden Tube-style 3D printers. These printers utilize a Bowden tube, a flexible tube that guides the filament from the extruder to the hot end, where it is melted and deposited onto the print bed. While the Bowden tube offers certain advantages, such as reduced weight on the print head and simplicity, it also presents some drawbacks worth considering.
One notable drawback is the increased susceptibility to filament clogs. The extended filament path within the Bowden tube introduces additional points where the filament can encounter obstacles or bends, potentially causing restrictions in filament flow. Restrictions can lead to disrupted extrusion and compromised print quality. Additionally, the travel distance between the extruder and the hot end can increase filament retraction requirements, further contributing to the likelihood of clogs.
Being aware of these inherent limitations is crucial when working with a Bowden Tube system. By understanding these potential challenges, users can take preventive measures and make informed decisions regarding filament selection, print settings, and maintenance routines. While Bowden Tube-style 3D printers offer certain benefits, weighing them against the potential issues associated with filament clogs and implementing strategies to mitigate them effectively is essential.
Now that we have examined the potential drawbacks of using a Boden Tube for filament feeding, we must explore the causes of filament clogs. Understanding these underlying factors is key to effectively preventing and troubleshooting clogs in 3D printers. Various factors can contribute to nozzle clogs. In the following section, we will detail these causes, providing practical solutions to address each one. Users can take proactive measures to ensure smooth and uninterrupted 3D printing by gaining insights into the typical culprits behind filament clogs. Let's now explore the causes of filament clogs and learn how to tackle them effectively.
Above Image: Hotend Cross Section from Creality Experts
Filament Clog Causes
Filament Contamination: Contaminants present in the filament can contribute to clogs. Poor-quality filament or improper handling and storage practices can introduce dust, debris, or moisture, eventually accumulating and obstructing the nozzle. To prevent filament contamination, always handle and store the filament in a clean and dry environment.
Heat Creep: Heat creep occurs when excessive heat travels upward through the hot end assembly, causing the filament to soften prematurely and clog the nozzle. Inadequate cooling or issues with the heat sink can contribute to heat creep. To prevent it, ensure proper hot-end cooling to maintain the heat sink's effectiveness.
Incorrect Filament Diameter: Filament diameter consistency is crucial for smooth extrusion. Variations in filament diameter can cause the extrusion system to become imbalanced, leading to nozzle clogs. Always verify the filament diameter and adjust the printer settings to ensure a proper flow.
Partially Molten Filament: Build-up During 3D printing, the partially molten filament can accumulate and gradually build up inside the hot end, resulting in clogs over time. High extrusion temperatures or improper retraction settings can contribute to this filament build-up. Optimize your temperature and retraction settings to balance proper melting and controlled filament flow to minimize it.
Insufficient Retraction: Retraction pulls the filament back slightly to prevent oozing and stringing. Low retraction rates can leave filament residue behind, eventually causing clogs. Experiment with different retraction settings to find the optimal balance for your printer and filament.
Long Printing Sessions: Prolonged printing sessions can increase the risk of nozzle clogs. Heat accumulates as the printing process continues, and the filament may degrade or become more prone to clogging. Regular maintenance and periodic filament changes can prevent clogs during long print jobs. Consider implementing scheduled breaks to clean the nozzle and ensure smooth printing.
Nozzle Misalignment: Nozzle misalignment can also contribute to nozzle clogs. If the nozzle is not aligned with the heat break or there is damage to the nozzle or heat break, filament flow can be obstructed. Regularly inspect and align the nozzle to avoid potential clogging issues.
Now that we understand the causes of nozzle clogs and the impact of filament-related issues and mechanical faults let's examine how different filament characteristics influence their behavior and clog potential. Filament composition and properties are crucial factors that affect printability and present unique challenges. In the upcoming section, we'll explore filament types prone to clogs and the reasons behind their challenges.
Filament Type Clog Causes
Carbon Fiber Filament: Filaments infused with carbon fiber particles enhance printed parts' strength and rigidity. However, the abrasive nature of carbon fiber can accelerate nozzle wear and potentially lead to clogs. The carbon fiber particles can cause increased friction and generate more heat, resulting in filament residue accumulation and nozzle clogs over time.
Metallic Filament: Filaments containing metallic particles or metal-infused filaments, such as bronze or copper, can pose challenges due to their higher thermal conductivity and abrasive properties. The metallic particles can wear down the nozzle, leading to clogs and decreased print quality.
Wood Filament: Wood-infused filaments, composed of PLA or other base materials with wood particles, can create nozzle clogs due to organic matter. The wood particles can burn and leave residue accumulating in the nozzle, potentially causing clogs.
Flexible Filament: Flexible or elastomeric filaments, like TPU or TPE, have unique properties that make them prone to nozzle clogs if not properly handled. These filaments require precise extrusion settings, including slower print speeds and increased retraction, to prevent filament oozing or buckling within the nozzle.
High-Temperature Filament: Filaments designed for high-temperature printing, such as PEEK or PEI, often require specialized hot-ends and extruders. If not properly managed, these filaments can lead to clogs due to their higher melting temperatures and increased viscosity.
While these filament types have specific challenges, it's important to note that successful printing with these filaments is achievable with proper printer setup, appropriate settings, and maintenance practices. Understanding each filament type's characteristics and potential challenges is crucial for preventing nozzle clogs and ensuring consistent print quality.
Preventative Measures and Example
Preventive maintenance is critical to maintaining a reliable and efficient 3D printing experience, especially when preventing nozzle clogs. By implementing regular maintenance practices, you can significantly reduce the risk of clogs and ensure smooth printing operations. Taking a proactive approach to maintenance extends the lifespan of your 3D printer and contributes to consistent print quality. In the following section, we will delve into the essential preventive measures that can be taken to maintain a clog-free nozzle and optimize your printing sessions. Explore these maintenance practices to ensure a seamless and hassle-free 3D printing process.
Dirty neglected nozzle and hot end experiencing extrusion issues. Over-due for cleaning.
Residue from the melting process accumulates in every available space.
PTFE Bowden tube charred and deformed leaving space for molten plastic to accumulate. This charred section will be trimmed flush and cleaned.
Trimmed and cleaned PTFE tube ready for reassembly.
Reassembled and ready to print.
Preventive measures:
- Regularly clean the printer components, including the nozzle, heat sink, and extruder.
- Store filament in a dry and dust-free environment to avoid contamination.
- Verify and adjust filament diameter settings according to the manufacturer's recommendations.
- Implement proper cooling mechanisms to prevent heat creep and maintain optimal temperature conditions.
- Optimize retraction settings to minimize filament residue and prevent clogs.
- Consider using a larger diameter nozzle when working with higher clog-risk filaments. The larger nozzle diameter can reduce the likelihood of clogs and help mitigate the effects of nozzle wear. Remember to adjust the settings within your slicer software to compensate for the increased volume.
- Schedule regular maintenance sessions, including nozzle cleaning and inspection, to ensure smooth printing.
- Follow manufacturer guidelines and user recommendations for your specific printer model to maximize performance and prevent clogs.
Nozzle clogs on Bowden Tube style 3D printers can be frustrating but effectively addressed through preventive measures and proper filament selection. By understanding the causes of nozzle clogs, you can take proactive steps to mitigate these issues.
We hope this article has provided valuable insights into the causes of nozzle clogs and the preventive measures you can take to enhance your 3D printing experience. We're committed to supporting and empowering the 3D printing community, and we would love to hear from you. If you have any questions, suggestions, or topics you'd like us to cover in future articles, please comment below. Your feedback is invaluable in helping us tailor our content to your needs and interests. Let's continue to learn, explore, and grow together in the exciting world of 3D printing.
We look forward to reading your comments and incorporating your ideas into our upcoming articles.
Comments
-
Extremely useful info here! Thanks for sharing!
Categories
- All Categories
- 1 The Blog
- 1 What's Trending
- 7.7K The Community
- 3.1K General Discussion
- 128 New Members
- 830 Consumer Tech
- 214 Prebuilt PCs and Laptops
- 162 Software
- 31 Audio/Visual
- 51 Networking & Security
- 4 Home Automation
- 5 Digital Photography
- 13 Content Creators
- 29 Hobby Boards & Projects
- 80 3D Printing
- 83 Retro Arcade/Gaming
- 60 All Other Tech
- 345 PowerSpec
- 2.6K Store Information and Policy
- 147 Off Topic
- 52 Community Ideas & Feedback
- 610 Your Completed Builds
- 3.9K Build-Your-Own PC
- 2.8K Help Choosing Parts
- 326 Graphics Cards
- 334 CPUs, Memory, and Motherboards
- 141 Cases and Power Supplies
- 53 Air and Liquid Cooling
- 47 Monitors and Displays
- 90 Peripherals
- 64 All Other Parts
- 63 Featured Categories
We love seeing what our customers build
Submit photos and a description of your PC to our build showcase
Submit NowLooking for a little inspiration?
See other custom PC builds and get some ideas for what can be done
View Build ShowcaseSAME DAY CUSTOM BUILD SERVICE
If You Can Dream it, We Can Build it.
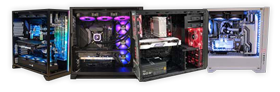
Services starting at $149.99