How to Install a Direct Drive Extruder
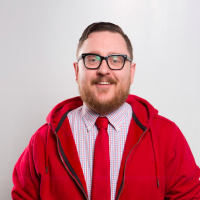
In 3D Printing, the end product is often a culmination of precise engineering and mechanics. One of the most crucial components in this process is the extruder. The extruder is responsible for feeding the filament, the primary material for printing, into the printer in a controlled and consistent manner. Its effectiveness and accuracy largely dictate the quality of the final printed object. Enter: the direct drive extruder
Direct Drive Extruders
The direct drive extruder is a specific type of extruder mechanism wherein the motor responsible for feeding the filament is located directly at the print head. This proximity allows for a more immediate and controlled extrusion of the filament.
For comparative understanding, consider the Bowden extruder. In a Bowden setup, the motor is distanced from the print head, necessitating the filament to traverse through an extended tube before reaching the hot end. While both the direct drive and Bowden systems have their merits, the proximity of the direct drive motor to the print head often affords a heightened precision in specific printing scenarios.
Advantages of Direct Drive Extruders
The direct drive extruder has garnered significant attention and adoption in the 3D printing community, and for good reasons:
- Increased Accuracy: Direct drive systems typically allow for a more precise filament feed. The short distance between the motor and the hot end means minimal room for error or inconsistency. This accuracy translates into finer print details.
- Reduced Filament Retraction Needs: Given the proximity of the motor to the print head, there's a notable reduction in the filament's retraction distance. This leads to faster response times and minimizes stringing or oozing between print moves, often resulting in cleaner prints.
- Superior Performance with Flexible Filaments: Direct drive extruders shine when printing with flexible materials. Bowden systems sometimes struggle with flexible filaments due to the longer filament path, which leads to bunching or jamming. The direct route in direct drive systems alleviates these issues, allowing for smoother Printing with materials like TPU.
Challenges and Limitations
- Increased Weight on the Print Head: A significant limitation of the direct drive system is the additional weight on the print head due to the motor's inclusion. This added weight can limit the achievable print speed and might result in slower movements, especially on larger printers.
- Potential for Increased Vibrations: The extra weight can also be a source of increased vibrations, particularly during rapid movement or direction changes. These vibrations can lead to artifacts in the print or reduced overall print quality in some scenarios.
- Other Challenges: Like all mechanical systems, direct drive extruders can face wear and tear. Their proximity to the hot end may also mean they're more susceptible to heat-related issues, requiring efficient cooling mechanisms to optimize performance.
While direct drive extruders offer notable advantages, especially in specific applications, balancing these benefits against their inherent challenges is essential. As with all tools, understanding the strengths and limitations of direct drive systems is crucial to harnessing their full potential effectively.
Upgrading to a Direct Drive System
With our understanding of direct drive extruders' multifaceted advantages and challenges, it's time to journey from theoretical knowledge to tangible application. Let's transition from the 'why' to the 'how,' guiding you meticulously through integrating the Creality direct drive kit with your Ender 3 V2 printer.
Preparation
Before upgrading to a direct drive system, you must prepare adequately. Having the right tools and a clear understanding of the process will make the installation smooth.
Tools and Materials:
- Tools provided by the kit
- Tweezers or pliers
- Creality direct drive extruder kit
- Zip ties or cable management tools (optional but recommended)
Safety Precautions:
- Always ensure the printer is powered off and unplugged before starting
- If you've recently used the printer, allow the hot end to cool down entirely
- Work in a well-lit area to ensure you can see and access all components
Installation Process
Dismantling the Existing Extruder Setup:
- Begin by carefully removing any filament loaded in the printer.
- Remove all zip ties (leaving the bowden tube attached).
- Slightly loosen the x-axis belts, detaching them from the bracket.
- Use a wrench on the eccentric spacer behind the lower wheel and loosen the roller. Use another wrench and a hex key to loosen the lower wheel until there's enough room to remove the extruder.
- Take note of any wires or connectors attached to the extruder motor and carefully disconnect them.
- Move on to the control board and wiring by removing the chassis' hardware. Remember, there are seven screws securing the control board to the chassis.
- Once you can access the control board, unplug the two main connectors: the thermistor and the filament cooling fan connector. After that, detach the hot end wires by unscrewing the terminals and gently pulling the wires out. Then, disconnect the red and black wires associated with the hot-end fan
- After cutting the zip tie that keeps the wire loom attached to the chassis, you can finally remove the extruder and prepare to install the new direct drive.
Installing the New Drive System:
- Start by threading the new extruder wires through the wire loom before making any connections.
- Connect the extruder fan to the terminal block, maintaining the same orientation as the original fan. Attach the hot end wires to the terminal block. Note that these aren't polarized and can be connected in any configuration.
- Connect the thermistor and the filament cooling fan plugs to the control board.
- Before sealing the chassis, inspect your wiring and cable layout. Ensure a new cable tie secures the wire loom to the chassis.
- Carefully attach the chassis screws back, ensuring the control board is firmly secured to the main chassis. Pro-tip: Always place hardware finger-tight before fully securing all hardware.
- Upright your printer and carefully position the new direct drive extruder in its place. Fine-tune the eccentric spacer for a snug fit. Slide and roll the extruder to confirm smooth movement.
- Attach the drive belts back to the bracket and tighten the belt by adjusting the belt adjuster knob.
- Disconnect the stepper motor control plug and attach the extension cable. You can then remove the original extruder stepper motor.
Troubleshooting and Challenges:
- Misalignment: If the extruder isn't sitting flush with the mount, double-check to ensure you've used the correct screws and mounting holes.
- Connectivity Issues: Recheck all wire connections if the motor doesn't respond once powered on. Ensure they are firmly connected and in their correct spots.
- Filament Feeding Issues: If the filament doesn't feed smoothly, ensure the hobbed gear of the direct drive system is tight enough.
Post-Installation Checks
Functionality Test:
- With the printer powered off, manually feed the filament through the direct drive system. It should move smoothly without any hitches.
- Initiate a small test print. Observe the filament flow and retraction to ensure the new system works correctly.
Calibration and Adjustments:
- It's advisable to recalibrate your printer after such an upgrade. Run a bed leveling test and adjust as necessary.
- Considering the direct drive system's characteristics, you might also need to adjust retraction settings. Start with lower retraction distances and tweak as per the results. This was the first print with the new setup, and you can see globing and stringing is a problem with the current settings.
While upgrading to a direct drive system can feel daunting, a systematic approach and careful preparation can make the process manageable. Ensure you always refer to the manual specific to your 3D printer model, as there may be model-specific nuances to be aware of during the upgrade.
To every avid 3D printer enthusiast reading this, the realm of direct drive extruders beckons with open arms. The opportunity to enhance print quality, explore flexible materials, and overall refine the printing process is just an upgrade away. So, as you embark on your next 3D printing project, consider the direct drive route. Embrace the innovation, harness its capabilities, and let your prints stand as a testament to the precision and quality a direct drive system can offer.
In essence, 3D Printing is as much about exploration as it is about creation. So, dare to explore, dare to innovate, and above all, dare to p
Comments
-
Very informative
-
another great tutorial
-
I love the way you explained everything.
-
This is very helpful! I will definitely reference this next time!
-
Will attempt this soon. Thank you for the guide!
-V
Categories
- All Categories
- 1 The Blog
- 1 What's Trending
- 7.7K The Community
- 3.1K General Discussion
- 130 New Members
- 832 Consumer Tech
- 215 Prebuilt PCs and Laptops
- 163 Software
- 31 Audio/Visual
- 51 Networking & Security
- 4 Home Automation
- 5 Digital Photography
- 13 Content Creators
- 29 Hobby Boards & Projects
- 80 3D Printing
- 83 Retro Arcade/Gaming
- 60 All Other Tech
- 350 PowerSpec
- 2.6K Store Information and Policy
- 148 Off Topic
- 52 Community Ideas & Feedback
- 612 Your Completed Builds
- 3.9K Build-Your-Own PC
- 2.8K Help Choosing Parts
- 326 Graphics Cards
- 334 CPUs, Memory, and Motherboards
- 141 Cases and Power Supplies
- 54 Air and Liquid Cooling
- 47 Monitors and Displays
- 90 Peripherals
- 64 All Other Parts
- 64 Featured Categories
We love seeing what our customers build
Submit photos and a description of your PC to our build showcase
Submit NowLooking for a little inspiration?
See other custom PC builds and get some ideas for what can be done
View Build ShowcaseSAME DAY CUSTOM BUILD SERVICE
If You Can Dream it, We Can Build it.
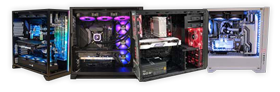
Services starting at $149.99