Using LightBurn with the TOTEM S Laser
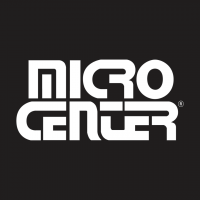
LightBurn is one of two software packages recommended for controlling Two Trees’ TOTEM S laser. LightBurn is a powerful software package that includes basic CAD functionality, support for most vector files including .pdf, .ai, and .dxf, and support for a wide range of laser controllers. Unlike LaserGRBL, it’s neither free nor open source. That said, LightBurn’s features are worth the $60-$120 price tag.
Before heading over to LightBurn’s website to purchase a license, you’ll want to make sure you understand the license scheme. LightBurn offers versions of their license: GCode and DSP, which are priced at $60 and $120 respectively. The DSP license can do everything the GCode license can, but adds support for DSP controllers such as Ruida. If you purchase the GCode license you have the option to upgrade to a DSP license in the future for $60. Both licenses are perpetual licenses that include one year of updates. This means you can keep using LightBurn forever without renewing your license, but you will not be able to update the software after one year. For $30 you can renew your license and receive another year of updates. There’s also a 30 day trial so you can decide if you like the software well enough to buy it.
If you only intend to use LightBurn for the TOTEM S or other GCode laser cutters I recommend purchasing the GCode license to save a bit of money. In general, GCode controllers are found in open frame diode lasers and DSP controllers are found in fully enclosed fiber and CO2 lasers. If you end up purchasing a laser with a DSP controller in the future you can upgrade your license for $60.
Open frame lasers like the TOTEM S on the left tend to use GCode controllers. Enclosed lasers, like the CO2 laser on the right, are more likely to use DSP controllers.
After buying a license your key will be emailed to you. Download LightBurn using the links here, and install it. You will be asked for your license key on the first run.
With LightBurn installed and licensed we can get a new laser created. You’ll be required to create a new laser on the first run. In the device window click “Create Manually” to launch the new device wizard.
Next, select GRBL as the controller.
You’ll only have one option for connection: Serial/USB.
Next, name your device (I chose GRBL) and enter 300mm for the X and Y axis lengths.
Set the origin point to Front Left and disable auto home on startup:
Finally, verify the settings and click “Finish”.
That’s all there is to setting up the software. Connect your laser to your computer via USB. In the lower right side of the screen you’ll see a block that’s named “Laser”. In this block is a button that says “Devices” and two drop down menus. Make sure your device name is selected in the second drop down and the appropriate COM port for your laser is selected in the first drop down.
Next, you’ll need a file to cut. You can draw shapes with the tools on the left side of the window, or import a file by clicking “File” then “Import”. I usually design my files in Illustrator then import them into LightBurn.
Importing files allows you to take advantage of powerful CAD and design programs like autoCAD and Illustrator.
In the upper right is a block titled “Cuts/Layers”. “Layer” in LightBurn is another name for color. We’ll use different colors to separate parts of our file that will be processed with different settings or in specific orders. For example, in the file below the yellow areas will be engraved and the blue lines will be cut:
In this file, everything will be cut at the same speed and power. However, I wanted the small circles to cut first in case the larger shape shifts after it is cut. I used two different colors to give me control over the order:
LightBurn doesn’t care what colors or color space you use, whether shapes are filled or not, or what stroke widths are used on lines.
Once your file is imported or created, double click on one of the layers in the top right. This will open the cut settings editor window where we can input cut or engrave settings. Start by selecting the appropriate mode from the dropdown menu. There’re 4 options, but we’ll only be going over Line and Fill as they are the most useful modes for cutting and engraving. We’ll start with Line, which is used for cuts. Line traces a vector path.
Double click any layer in this block to open the cut setting editor
Starting from the top of the window and working down we’ll enter our cutting parameters. We can’t change the Layer color without changing our file. The Name isn’t important, but can be useful to keep track of layers in complex files. Speed and Power are two of the most important settings. These settings have the biggest impact on the thickness of material you can cut. Low speed and high power will cut through thicker materials like plywood, but might burn thinner materials like paper. High speed and low power won’t cut through plywood, but will give better results on thin material. For 3mm plywood I found 8mm/sec at 100% power works well. Next to the Speed and Max Power boxes are two toggle switches. One is named Output. If this switch is off the layer you have selected will not be processed when the laser is running, so make sure it’s on. The next switch, Air Assist, doesn’t matter because the TOTEM S does not have an air assist.
Speed, power, and mode are our most important settings.
Moving down to the next block we get into some more advanced settings. Start and end pause time are typically unnecessary for diode lasers. Kerf offset can be useful to ensure a tight fit between parts. The laser takes away about .005” of material as it cuts, so offsetting your path by a few thousandths of an inch can help make parts snap together. I frequently use this setting when making inlays. Number of passes is also important for cutting. Using the settings for 3mm plywood I listed above, I found I needed 13 passes to reliably cut 3mm plywood. Overcut is the distance the beginning and end of a path will overlap. I’ve been leaving this at 0 for the TOTEM S, but typically use about .015” of overcut on my other lasers.
Number of passes is the most important setting here. The rest can usually be left at their default value.
The remaining settings can usually be left off. For information on these settings, check out LightBurn’s documentation.
These settings are rarely used. Check the LightBurn documentation for more information on them.
Now that our cut is set up, we’ll start looking at some engraving settings. To change to another layer, just click the colored box on the left side of the cut settings editor. We’ll set this layer to fill. Fill fills the area encompassed by a vector path.
Like before, we’ll start at the top and move down. Layer can’t be changed without changing the file, and Name isn’t terribly important. Once again, Speed and Power are the most important settings. For engraving, we typically run at higher speeds and lower powers since we don’t want to go all the way through. I found 200mm/sec and 100% power worked well on plywood. Just like Line, we want output on and don’t care about Air Assist.
We’re going to jump around a bit in the Fill Settings block because some settings are closely related but not in order. First, near the bottom, you’ll find Number of Passes. For really deep engravings you might want more than one pass, but one is usually adequate. Next, we’ll jump back to the switches at the top. First is Bi-directional fill. With this enabled, the laser will fire while moving left and right. If it’s disabled it will only fire while moving to the right. Next is Cross-Hatch. With this enabled the laser will do two passes, and the second pass will be rotated 90 degrees relative to the first pass. Jumping past Line Overscanning, Line Interval, and Lines per Inch we find Scan Angle. This changes the angle of motion of the head. As you change these settings the block of arrows to the left will move to indicate how the head will move. I recommend leaving Bi-directional fill on, Cross-Hatch off, and Scan Angle at 0. This will give you the fastest processing times.
Line Interval and Lines per Inch are two ways to talk about the distance the head moves in between lines. If you change one the other will automatically change too. 250 lines per inch is a good all-around setting. It balances speed and quality nicely. For high-quality engraving, I might go as high as 500 lines per inch. For quick, draft-quality engraving I’ll go down to 100 or 150 lines per inch.
From left to right, this image shows 500 lines per inch, 250 lines per inch, and 100 lines per inch on .5” circles.
Overscanning and ramp length can generally be left off and at 0 respectively.
Near the bottom is a group of 3 radio buttons. These affect how shapes are grouped while the laser is running. If “Fill all shapes at once” is selected the laser will move to and fire on every shape in the same line in a single pass. This works well for shapes that are close together, but can be slow for shapes spaced far apart. “Fill shapes individually” will fill a shape in its entirety, then move to the next shape even if they are in the same line. “Fill groups together” will fill a group of shapes in its entirety then move to the next group. See the animation below for an example.
From top to bottom, this video shows “Fill all shapes at once”, “Fill shapes individually”, and “Fill groups together”. Note that I manually grouped the last line into pairs for this demonstration.
Once again, the rest of the settings can generally be left at their default values. Check out the documentation if you want information on them.
Now that all our settings have been entered, click Okay at the bottom of the cut setting editor. If you want to rearrange your layers so they run in a different order, you can select a layer in the Cuts/Layers block and use the arrows on the right to move the layer up or down. In general it’s best to engrave first and cut from the inside out.
The arrows on the left allow you to reorder layers.
We’re almost ready to start cutting. Make sure your laser is plugged into your computer and powered on. Next, move the head to the point you want to start from. This can be a corner, the middle, or the center of an edge. Use the Job Origin radio buttons in the Laser block of LightBurn to select your origin point, and make sure the Start From drop down is set to Current Position.
Use the Job Origin radio buttons to change where the laser starts a job
Before cutting it’s a good idea to frame your job. LightBurn offers a rectangular frame which traces a bounding box around your job, and a rubber band frame which closely follows the outermost line of your job. Click either one and your laser head should start moving. Ensure the head doesn’t move off your material. If it does move off the material, reposition your material or head and make sure you have the correct Job Origin selected. If the head doesn’t move ensure the machine is powered on, connected via USB, and you have selected the correct COM port and device.
The frame buttons help ensure your job won’t fall outside of your material
Finally, attach the red laser guard included with the TOTEM S to the laser source and focus the laser using the silver Z height knob. I set mine to about 1mm above my material. Now that our file and laser are set up, it’s time to cut. Don your green safety glasses and click the Start button. You’ll get a warning about the job potentially being outside the cut area. As long as you have framed your job and are sure it will fit in the area you have to work with you can safely ignore this warning. The laser will start processing your job in the order you set in the Cuts/Layers block.
Click “Start” to begin processing a job.
The most common question I get in my laser classes is “what settings should I use?”. This is an extremely difficult question to answer. I can guess starting settings for materials and lasers I have used extensively, but that’s based entirely on my experience with a particular material and machine. The best option is to get more material than you need and run some test cuts at various power and speed settings until you find something that works well. If you want to make an engraving deeper or didn’t cut all the way through your material, try slowing down the speed, increasing the number of passes, or increasing power. On the other hand, if you find your cuts are charring the back or your engraving is too deep, try increasing speed, decreasing number of passes, or decreasing power. As you use the machine you’ll start to get a feel for where you should start and how changes to your settings will affect your results. Test cards like these from brento1 on Thingiverse can help. Note these are intended for CO2 lasers, so you’ll need to modify the settings to use them on a diode laser.
Tests cards like these can speed up the process of finding perfect settings
If you’re looking for a free and open-source option for controlling your TOTEM S, keep an eye out for my next article on running the laser using laserGRBL. In the future, we’ll also look at how the TOTEM S handles processing a range of materials and designing files for laser cutting. And if you missed last week, we cracked open and gave our first impression of the fantastic TOTEM S Diode laser!
Looking for more Maker guides and reviews? We’ve got a 3D Printing Community as well as a Maker Community, a whole section of 3D Printing How-Tos, as well as articles on How to Choose a 3D Printer and Raspberry Pi set-up guides. And if you can’t find what you’re looking for, don’t hesitate to post a new discussion and the Community will be happy to help!
Categories
- All Categories
- 1 The Blog
- 1 What's Trending
- 7.7K The Community
- 3.1K General Discussion
- 130 New Members
- 832 Consumer Tech
- 215 Prebuilt PCs and Laptops
- 163 Software
- 31 Audio/Visual
- 51 Networking & Security
- 4 Home Automation
- 5 Digital Photography
- 13 Content Creators
- 29 Hobby Boards & Projects
- 80 3D Printing
- 83 Retro Arcade/Gaming
- 60 All Other Tech
- 353 PowerSpec
- 2.6K Store Information and Policy
- 148 Off Topic
- 52 Community Ideas & Feedback
- 612 Your Completed Builds
- 3.9K Build-Your-Own PC
- 2.8K Help Choosing Parts
- 326 Graphics Cards
- 334 CPUs, Memory, and Motherboards
- 141 Cases and Power Supplies
- 54 Air and Liquid Cooling
- 47 Monitors and Displays
- 90 Peripherals
- 64 All Other Parts
- 64 Featured Categories
We love seeing what our customers build
Submit photos and a description of your PC to our build showcase
Submit NowLooking for a little inspiration?
See other custom PC builds and get some ideas for what can be done
View Build ShowcaseSAME DAY CUSTOM BUILD SERVICE
If You Can Dream it, We Can Build it.
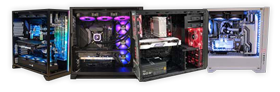
Services starting at $149.99