Making an Eco-Friendly 3D Printer Ecosystem
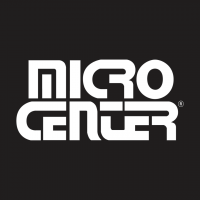
3D printing is a wonderful technology that has revolutionized rapid prototyping, small-scale manufacturing, and allowed individuals to produce custom products on a one-off basis. But, like any technology, it isn’t without its hiccups. Packaging and failed prints can produce plastic waste, and running a 3D printer inefficiently can cost energy. Thankfully, though, there are a few simple ways you can make your 3D printing ecosystem eco-friendly!
Recycling Packaging and Spools
Traditionally, filament comes in packages on injection molded plastic spools. These spools are lightweight, inexpensive, and durable. However, these spools aren’t always recyclable. Some are made from materials that can’t be recycled. Some are made from recyclable materials but are not accepted by municipal recycling programs because they are unmarked. Even if a spool is recyclable, there is a limit to the number of times it can be recycled before deteriorating beyond the point of usefulness. Thankfully, there is a lot that can be done with these plastic spools instead of just sending them to the landfill.
Plastic spools can be reused for a number of purposes. They’re great for storing Christmas lights and short extension cords. You can use your 3D printer to print drawers that fit in a filament spool, like these from Thingiverse user MistrYpsilon. You can stack them or glue them together and use them as small storage shelves. But even with all these possible uses, we all end up with more spools than we need eventually. Enter: cardboard spools.
Empty spools can be a great start for many organization projects.
Cardboard spools are nothing new, but they are becoming more common. Protopasta and other companies have been using cardboard spools for years, and Inland PLA is now available on cardboard spools. Durability is often cited as a concern with these spools, but I have not experienced any issues with cardboard spools. Protopasta uses corrugated cardboard, while Inland uses solid cardboard, and both have worked easily with my printer. And cardboard can easily be recyclable in all areas and breaks down much faster than plastic if it must be sent to a landfill. But if you don’t want to use a spool at all, there’s also spooless filament.
Inland’s filament now comes on an easily recycled cardboard spool
Spooless filament is another option for reducing the number of spools used. While trying to print without a spool tends to end poorly, there are a number of options for reusable spools the spooless filament can be loaded onto. These spools are made of 2 or more pieces allowing them to be disassembled to load new filament. Micro Center carries this spool made by Inland, or you can print your own using a model like this one from Thingiverse user danielbeaver. Spooless filament reduces waste by only requiring one spool for an infinite amount of filament. Spooless filament tends to be slightly cheaper per kilogram as well. Factoring in the cost of the reusable spool, printing with spooless filament becomes cheaper than printing with spooled filament after 3kg.
Spooless filament doesn’t come on a spool, but it’s easily loaded onto a commercial or 3D printed spool.
If you still have a surplus of plastic spools, you may be able to turn your spools into a filament manufacturer for reuse. The Columbus-based filament company IC3D accepts spools from IC3D, Printed Solid, and Inland filament in exchange for a discount on their recycled PETG filament. They don’t run this program all the time, so you may need to check their website or sign up for their newsletter to be notified when the program is open. You can find more information about this program here.
Reusing Extra Print Materials
While the steps above help reduce the waste from packaging 3D filament, they don’t help with the waste created by failed prints, supports, and prototypes. Unfortunately, most plastics used in 3D printing are not recyclable through municipal recycling programs. PLA, ABS, nylon, and polycarbonate are not recyclable through most municipal recycling programs. Polypropylene can be recycled in some municipalities, but few people use it for 3D printing. While PETG is chemically similar to the recyclable plastic PET, it’s typically not accepted for recycling as it is difficult to separate from PET and causes contamination. But all is not lost: there is still ways to recycle and reuse filament.
Some PLA is compostable, but generally only under industrial conditions. Backyard compost piles tend to be too cold for PLA to decompose. If your city offers composting as an option for waste disposal they may accept your PLA scraps. This can be a great way to keep plastic waste from ending up in the landfill.
If you’re careful to keep your scraps separated by material type, it’s possible to recycle them into usable filament at home. The process starts by taking sorted material and shredding it into small pieces. These pieces are then extruded through a hotend similar to the hotend on a printer. Once cooled, the extruded filament can be spooled up and used for future prints. There are a number of commercial and DIY options for recycling machines. Some integrate the shredder and extruder into one machine, though most require purchasing a shredder separately. With a powerful enough shredder, some of these systems can even be used to make filament from old spools.
Commercial options range from simple desktop units to larger production machines. Filabot is one of the most well-known commercial options for recycling filament at home. It’s a modular system that can be expanded to include a filament spooler and a cooling system. It takes about an hour to produce 1kg of filament on the Filabot. Alternatively, Wellzoom’s desktop filament extruder is a more entry-level option but takes a bit longer to produce 1kg of filament. Like the Filabot, Wellzoom offers an optional spooler. ReDeTec and 3Devo offer high-end desktop units for those who are really passionate about their prints and the environment.
When combined with a cooler and automatic spooler, the Filabot creates an efficient system for recycling filament.
You can also create your own, with DIY options ranging from kits that produce professional-looking systems to hardware store contraptions. The Felfil Evo is one of the more professional-looking options on the market. It can be expanded with a spooler and grinder to create an efficient system for recycling at home. It’s also available preassembled. Filastruder is one of the most well-known names in the home filament-making game and they offer a spooler to make winding your filament onto a spool easier. If you’re looking for a more hardcore DIY option, ianmcmill on Instructables has put together a guide on building an extruder from scratch.
Though a bit rough around the edges compared to some commercial offerings, ianmcmill’s DIY extruder is cheap and effective.
Reducing waste with print settings
It’s even possible to make your actual prints more eco-friendly! The default settings used in Cura and most other slicers are great for general-purpose printing but can be wasteful for some prints. When doing large prints that don’t need much strength like desk organizers or storage containers, you can often get away with dropping infill to 5% or 10%. This not only reduces the amount of material used but can dramatically reduce print time. Shorter prints equate to less energy used to run motors and heat beds and hotends.
Other than infill, the settings for these two prints are identical. Reducing infill from 20% to 7% cut print time by 7 hours and filament used by almost ⅓.
Reduce, Reuse, Recycle!
Reducing waste created by 3D printing doesn’t have to require big changes. Switching to filament that’s sold on cardboard spools or spooless filament doesn’t change your workflow, and might even save you money. For high-volume printers, a filament extruder can be a great way to reduce waste and provide a continuous source for filament that’s great for prototypes or other quick prints. Using efficient settings can help too. Reducing infill speeds up prints and reduces the amount of material used, both of which can reduce the environmental impact of 3D printing.
Looking for more information about Raspberry Pi? We’ve got a Hobby Board section of the community, as well as Hobby Board guides like The Definitive Micro Computer Buying Guide, Raspberry Pi Basics, and How to Create a Retro Game Console with Raspberry Pi! And if you can’t find what you’re looking for, don’t hesitate to post a new discussion and the Community will be happy to help!
Comments
-
good project for the weekend
Categories
- All Categories
- 1 The Blog
- 1 What's Trending
- 7.7K The Community
- 3.1K General Discussion
- 130 New Members
- 832 Consumer Tech
- 215 Prebuilt PCs and Laptops
- 163 Software
- 31 Audio/Visual
- 51 Networking & Security
- 4 Home Automation
- 5 Digital Photography
- 13 Content Creators
- 29 Hobby Boards & Projects
- 80 3D Printing
- 83 Retro Arcade/Gaming
- 60 All Other Tech
- 353 PowerSpec
- 2.6K Store Information and Policy
- 148 Off Topic
- 52 Community Ideas & Feedback
- 612 Your Completed Builds
- 3.9K Build-Your-Own PC
- 2.8K Help Choosing Parts
- 326 Graphics Cards
- 334 CPUs, Memory, and Motherboards
- 141 Cases and Power Supplies
- 54 Air and Liquid Cooling
- 47 Monitors and Displays
- 90 Peripherals
- 64 All Other Parts
- 64 Featured Categories
We love seeing what our customers build
Submit photos and a description of your PC to our build showcase
Submit NowLooking for a little inspiration?
See other custom PC builds and get some ideas for what can be done
View Build ShowcaseSAME DAY CUSTOM BUILD SERVICE
If You Can Dream it, We Can Build it.
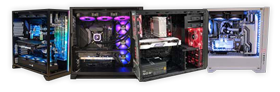
Services starting at $149.99